New method upcycles plastic waste to valuable productsNew method upcycles plastic waste to valuable products
Nanoparticles in catalytic solution breaks polycarbon bonds to create hydrocarbons for use in motor oil, liquids, detergents and more, researchers find.
October 25, 2019
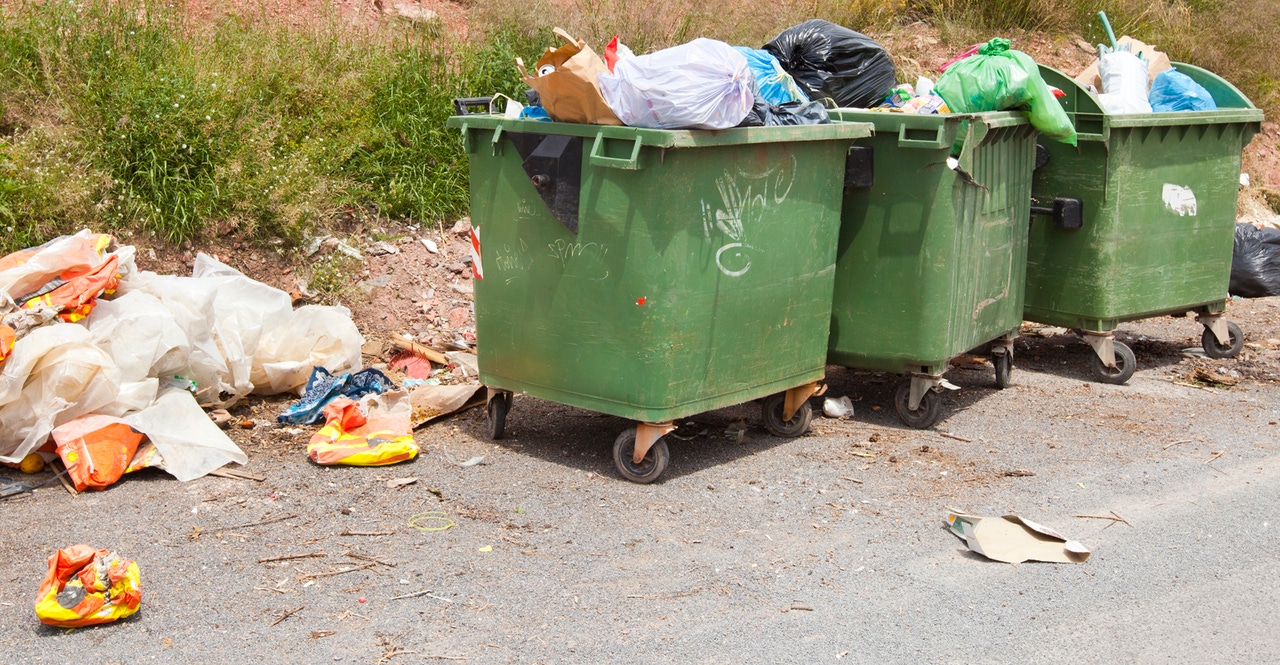
Researchers from Illinois and Iowa have developed a new method for upcycling abundant, seemingly low-value plastics into high-quality liquid products such as motor oils, lubricants, detergents and even cosmetics.
The catalytic method serves a one-two punch by removing plastic pollution from the environment and contributing to a circular economy. It also improves on current recycling methods that result in cheap, low-quality plastic products.
“Our team is delighted to have discovered this new technology that will help us get ahead of the mounting issue of plastic waste accumulation,” said Northwestern’s Kenneth R. Poeppelmeier, one of the project’s leaders. “Our findings have broad implications for developing a future in which we can continue to benefit from plastic materials, but do so in a way that is sustainable and less harmful to the environment and potentially human health.”
Poeppelmeier is the Charles E. and Emma H. Morrison Professor of Chemistry at Northwestern’s Weinberg College of Arts and Sciences. In addition, is the director of Northwestern’s Center for Catalysis and Surface Science and a member of Northwestern’s Program on Plastics, Ecosystems and Public Health.
Also leading the work were Aaron D. Sadow, a chemistry professor at Iowa State University and director of the university’s Center for Catalysis; and Massimiliano Delferro, leader of the Catalysis Science Program at Argonne National Laboratory.
The study, Upcycling Single-Use Polyethylene into High-Quality Liquid Products, was published Oct. 23 in the journal ACS Central Science. It was supported by the U.S. Department of Energy.
The plastic problem is expected to worsen
Each year, 380 million tons of plastic are created worldwide. And as the plastics market continues to increase, many analysts predict production could quadruple by 2050. More than 75% of these plastic materials are discarded after one use. Many of them end up in our oceans and waterways, harming wildlife and spreading toxins.
“There are certainly things we can do as a society to reduce consumption of plastics in some cases,” Sadow said. “But there will always be instances where plastics are difficult to replace, so we really want to see what we can do to find value in the waste.”
While plastics can be melted and reprocessed—molding park benches from used plastic bottles, for example—this method yields lower-value materials that structurally weaker than the original material.
When left in the wild or in landfills, plastics do not degrade because they have very strong carbon-carbon bonds. Instead, they break up into smaller plastics, known as microplastics. Whereas some people see these strong bonds as a problem, the researchers saw this as an opportunity.
“We sought to recoup the high energy that holds those bonds together by catalytically converting the polyethylene molecules into value-added commercial products,” Delferro said.
An electron micrograph of platinum nanoparticles deposited onto a perovskite nanotube.
The catalytic solution creates high-value products
The catalyst consists of platinum nanoparticles — just 2 nanometers in size — deposited onto a perovskite nanocubes, which are about 50-60 nanometers in size. A nanometer equals one-billionth of a meter. For perspective, if the Earth’s diameter was 1 meter, the diameter of a marble would equal 1 nanometer, according to the National Nanotechnology Initiative.
The team chose perovskite—a mineral made of calcium, titanate and oxygen—because it remains stable under high temperatures and pressures and is an exceptionally good material for energy conversion.
To deposit nanoparticles onto the nanocubes, the team used atomic layer deposition, a technique developed at Argonne that allows precise control of nanoparticles.
Under moderate pressure and temperature, the catalyst cleaved plastic’s carbon-carbon bond to produce high-quality liquid hydrocarbons. These liquids could be used in motor oil, lubricants or waxes or be processed more to make ingredients for detergents and cosmetics. Currently, commercially available catalysts generate lower quality products with many short hydrocarbons, which limit the products’ usefulness.
Importantly, this catalytic method produced far less waste. Recycling methods that melt plastic or use conventional catalysts generate both greenhouse gases and toxic byproducts.
The study’s authors are Gokhan Celik, Robert M. Kennedy, Ryan A. Hackler and Magali Ferrandon, all of the Argonne National Laboratory’s Chemical Science and Engineering Division, Lemont, Illinois; Akalanka Tennakoon, Smita Patnaik and Marek Pruski of Iowa State University and Ames Laboratory, Ames, Iowa; and Frédéric A. Perras of Ames Laboratory, Ames Iowa.
Also, Anne M. LaPointe, Department of Chemistry and Chemical Biology, Cornell University, Ithaca, New York; Salai C. Ammal and Andreas Heyden, both of the Department of Chemical Engineering, University of South Carolina, Columbia, South Carolina; Susannah L. Scott, Department of Chemical Engineering, Santa Barbara, California; as well as Ppoeppelmeier, Sadow and Delferro.
Source: Northwestern University
You May Also Like